NEWCOLD ADVANCED LOGISTICS
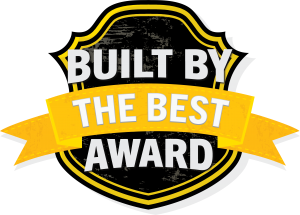
Built By The Best Award
Winner of GCCA’s Built by the Best Award – 2018. Given by the Controlled Environments Building Association, CEBA, the award is given in recognition of outstanding contractor performance.
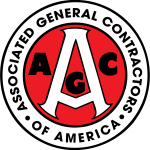
Associated General Contractors — 2019
Winner of multiple Associated General Contractors – 2019 Build Washington Awards.
Project Description
Client: NewCold Advanced Logistics
Location: Tacoma, Washington
Size: 310,000 sq. ft.
Facility Type: Automated Storage Retrieval System (ASRS) | Distribution
Fisher Builds ‘Cold Storage of the Future’
Maximizing Space, Energy & Reliability
Using state-of-the-art technology throughout the facility, the ASRS system uses robotic conveyors to store, move and retrieve products throughout in the low-oxygen high-bay warehouse. The robots and conveyor equipment are directed by operators using Newcold’s advanced proprietary software system, keeping products in optimal conditions with the entire cold storage cooled to sub-zero temperatures.
NewCold Tacoma represents the future in cold storage warehouse construction. The facility marks the first step into the US market for the European-based logistics company. The freezer and office were designed in tandem with NewCold and built by Fisher.
On a footprint of 242,000 sf, the freezer boasts a volume of nearly 25M cubic feet of storage. Enough to fill Seattle’s century link field. The facility also represents a game-changing solution to cold storage with its low-oxygen high bay freezer. Not to mention, the automated storage and retrieval system (ASRS).
Product is stored in NewCold’s thermal tight freezer, where oxygen is reduced to 16.5% saturation. Thus, eliminating the possibility of fire and allowing the 135’ high product storage. Robotic cranes and conveyors are deployed throughout the facility’s intricate racking system. Delivering products to the loading dock, where they are loaded on to trucks, all without breaking the thermal cold chain.
Although not a new construction technique, building a rack supported structure as a high-bay cold storage is highly innovative. Free of traditional building supports, horizontal and vertical conveyors run unobstructed through the warehouse, maximizing storage density. This higher-density, lower-footprint configuration radically reduces energy costs normally associated with frozen food storage. In fact, the freezer operates on half the energy needed by a conventionally built cold storage.
As with any project, success depends on a high degree of organization, cooperation, and communication. Fisher possess an unrelenting commitment to the details required to bring a facility online. As a result, they have been awarded with additional NewCold projects.